Hydraulic seals play a vital role in the functionality and efficiency of hydraulic systems. As the backbone of many industrial applications, these seals are designed to prevent fluid leakage and maintain pressure within hydraulic circuits. In this blog, we will explore the basics of hydraulic seals, their types, and their importance across various industries.
At its core, a hydraulic seal is a device that creates a barrier between two surfaces, ensuring that hydraulic fluid remains within the system. This seal is critical to the proper functioning of hydraulic machinery, which relies on pressurized fluid to transmit power. Without effective seals, hydraulic systems will leak, leading to reduced efficiency, increased wear and potential system failure.
There are many types of hydraulic seals, each designed for specific applications and conditions. The most common types include O-rings, rod seals, and piston seals. O-rings are versatile and can be used in a variety of configurations, while rod seals are specifically designed to prevent leakage in hydraulic cylinder rods. Piston seals, on the other hand, are used to seal the piston within the cylinder to ensure optimal performance.
The materials used for hydraulic seals are equally important. They must be durable and resistant to wear, temperature fluctuations, and chemical corrosion. Common materials include rubber, polyurethane, and PTFE (Teflon), each with unique properties suitable for different environments.
In summary, hydraulic seals are important components that ensure the reliability and efficiency of hydraulic systems. Understanding their functions and the various types available can help industries select the right seals for their specific needs, ultimately improving the performance and life of hydraulic equipment. As technology advances, the development of more efficient and durable hydraulic seals will continue to enhance the functionality of hydraulic systems across i

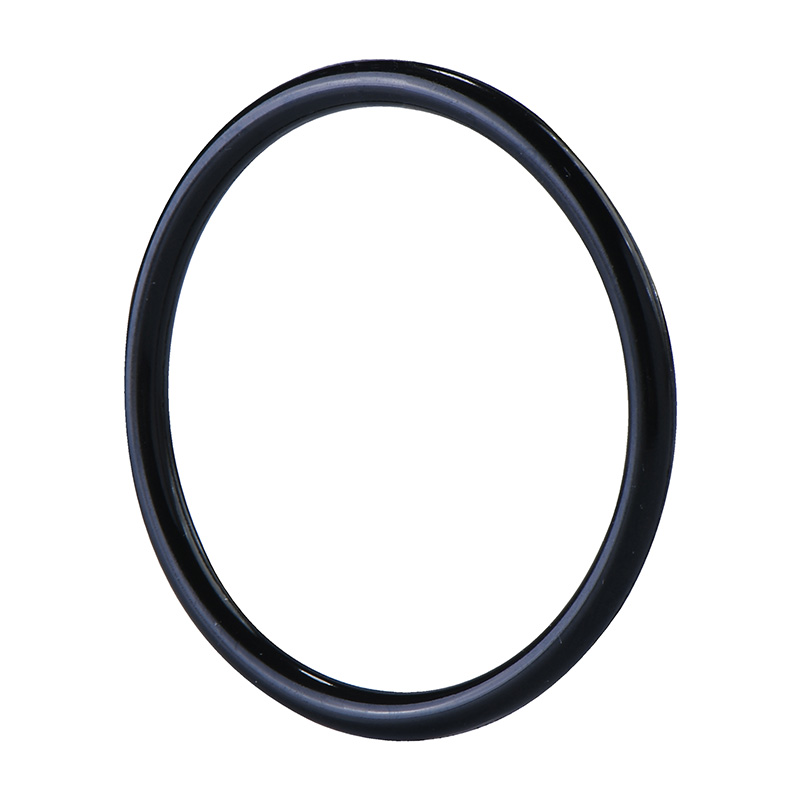
Post time: Dec-13-2024